BIG Manufacturing Consulting
Increase Profitability Through Meaningful
System and Cultural Improvements
BIG Manufacturing Consulting
Increase Profitability Through Meaningful System and Cultural Improvements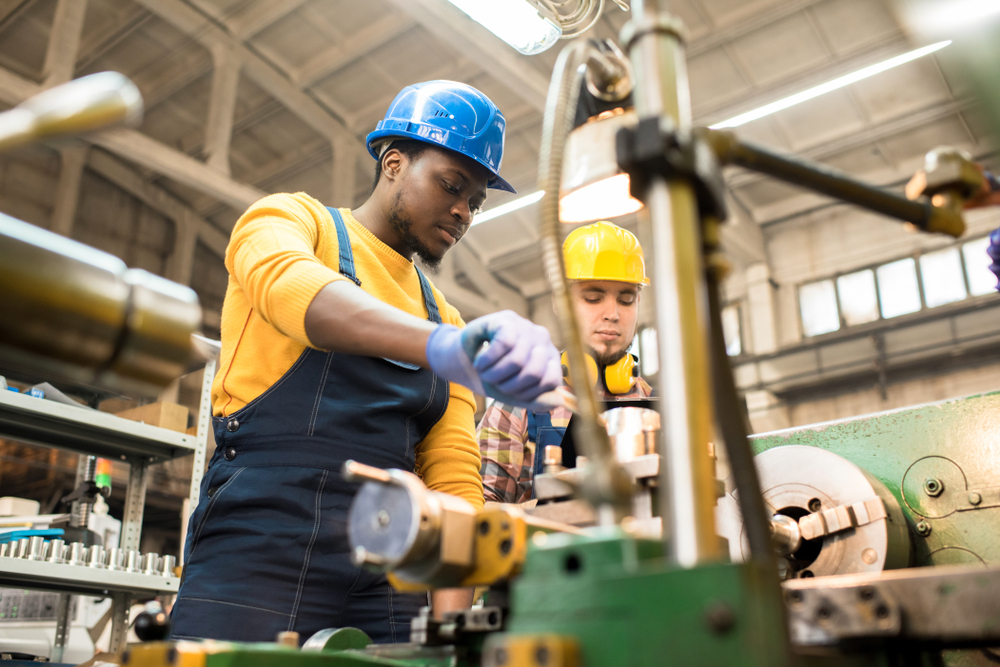
Our Consulting Approach
As a training and consulting company, we work with and train an intitial “pilot team” when approaching a project. The team will then work together on the following:
- Baseline the current-state system
- Analyze the production line (with the aid of our Total Analysis Software Package)
- Suggest possible process improvement solutions and ways to eliminate waste & ergonomic/safety concerns
- Implement the new process and create a set of standard steps utilizing industrial engineering standards
- Check the status post-implementation, then develop & coach Lean Leadership skills to the supervisors with a focus on “Respect for Humanity”
- Sustainment tools are embedded into the system in order to ensure continued succes
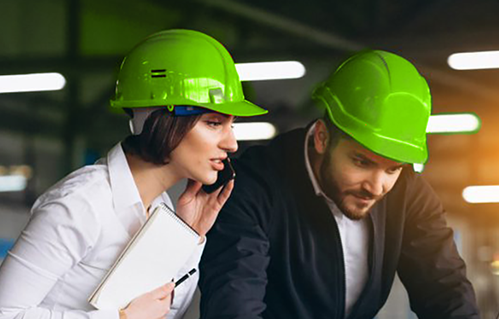
BIG Business Assessments
Options range in duration from a plant visit and informal report to a fully documented week long assessment
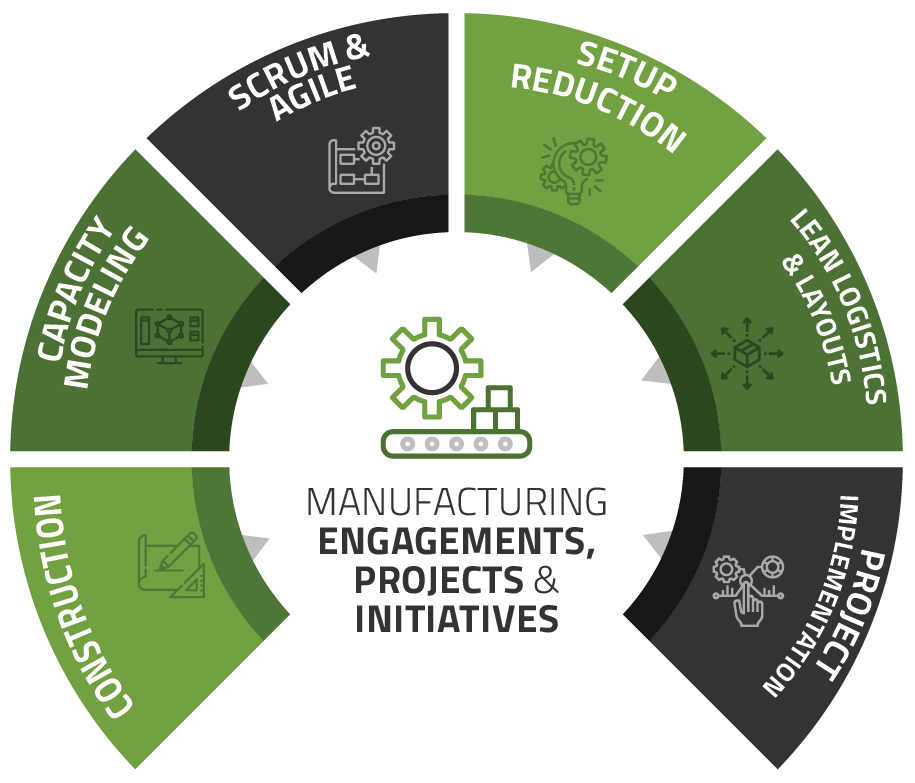
One-on-One Advising and Mentorship
Our Consulting Approach
As a training and consulting company, we work with and train an intitial “pilot team” when approaching a project. The team will then work together on the following:
- Baseline the current-state system
- Analyze the production line (with the aid of our Total Analysis Software Package)
- Suggest possible process improvement solutions and ways to eliminate waste & ergonomic/safety concerns
- Implement the new process and create a set of standard steps utilizing industrial engineering standards
- Check the status post-implementation, then develop & coach Lean Leadership skills to the supervisors with a focus on “Respect for Humanity”
- Sustainment tools are embedded into the system in order to ensure continued success.
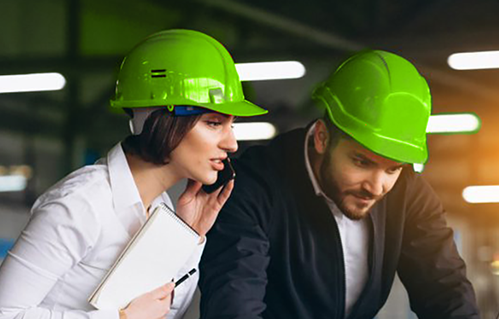
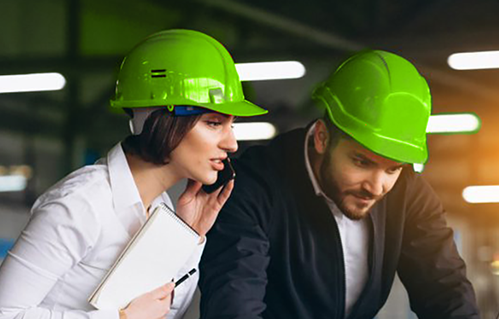
BIG Business Assessments
Options range in duration from a plant visit and informal report to a fully documented week long assessment.
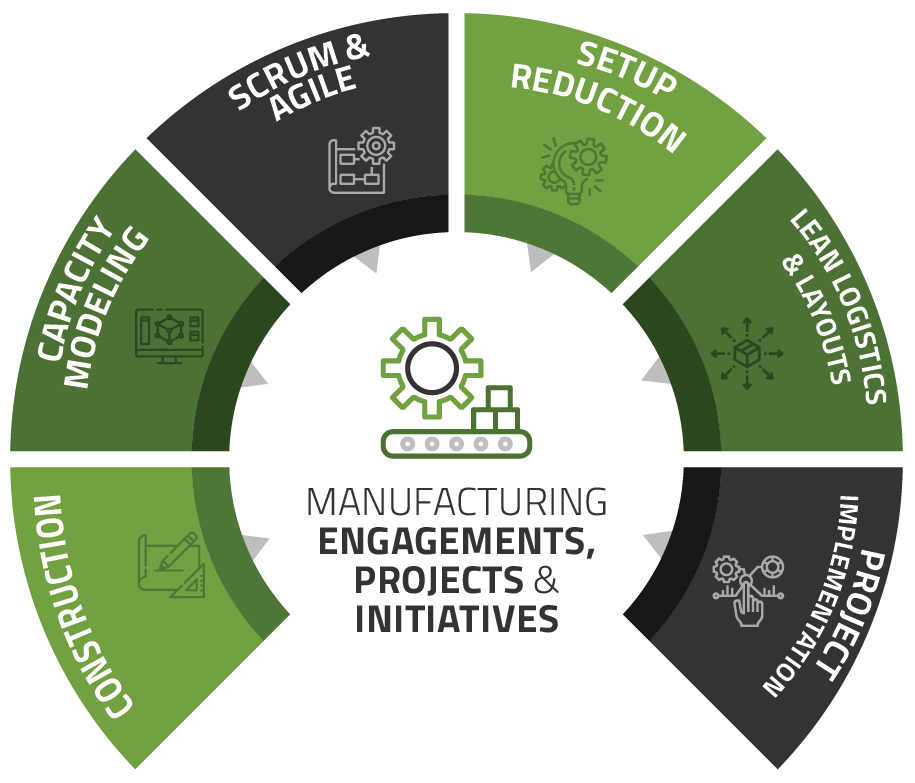
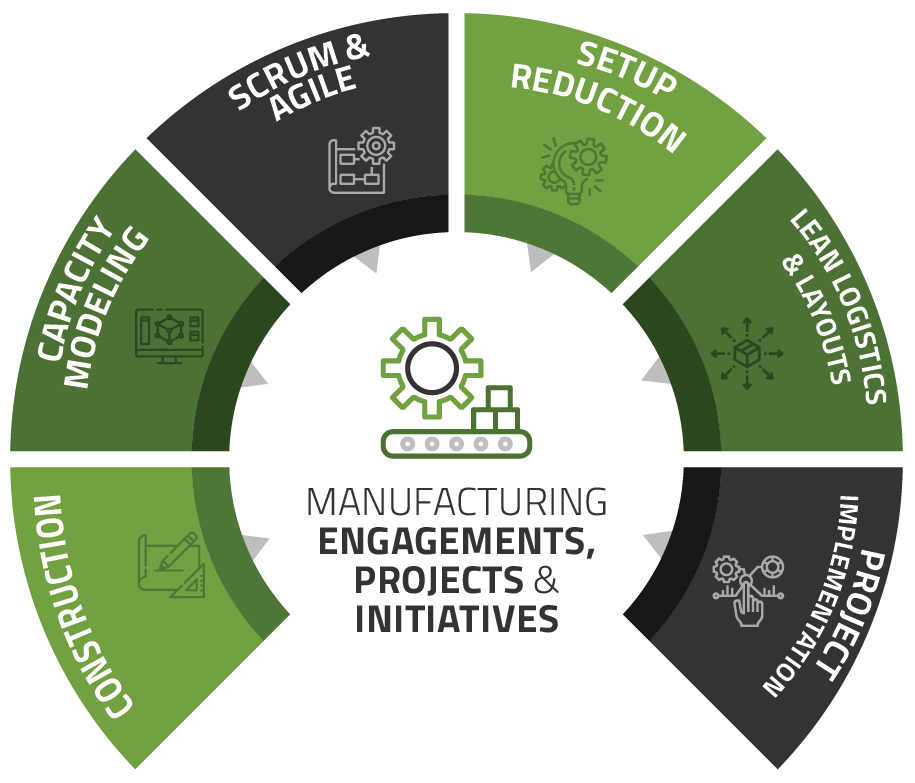
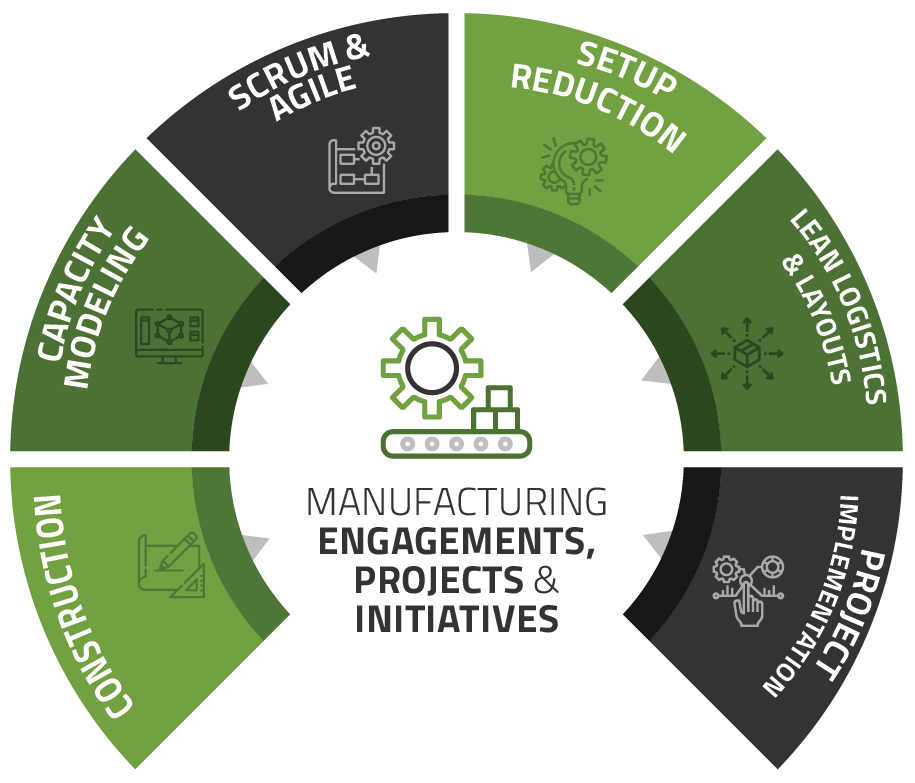
One-on-One Advising
& Mentorship
Examples of Some of our Clients
Lead Contact For Manufacturing Operational Excellence
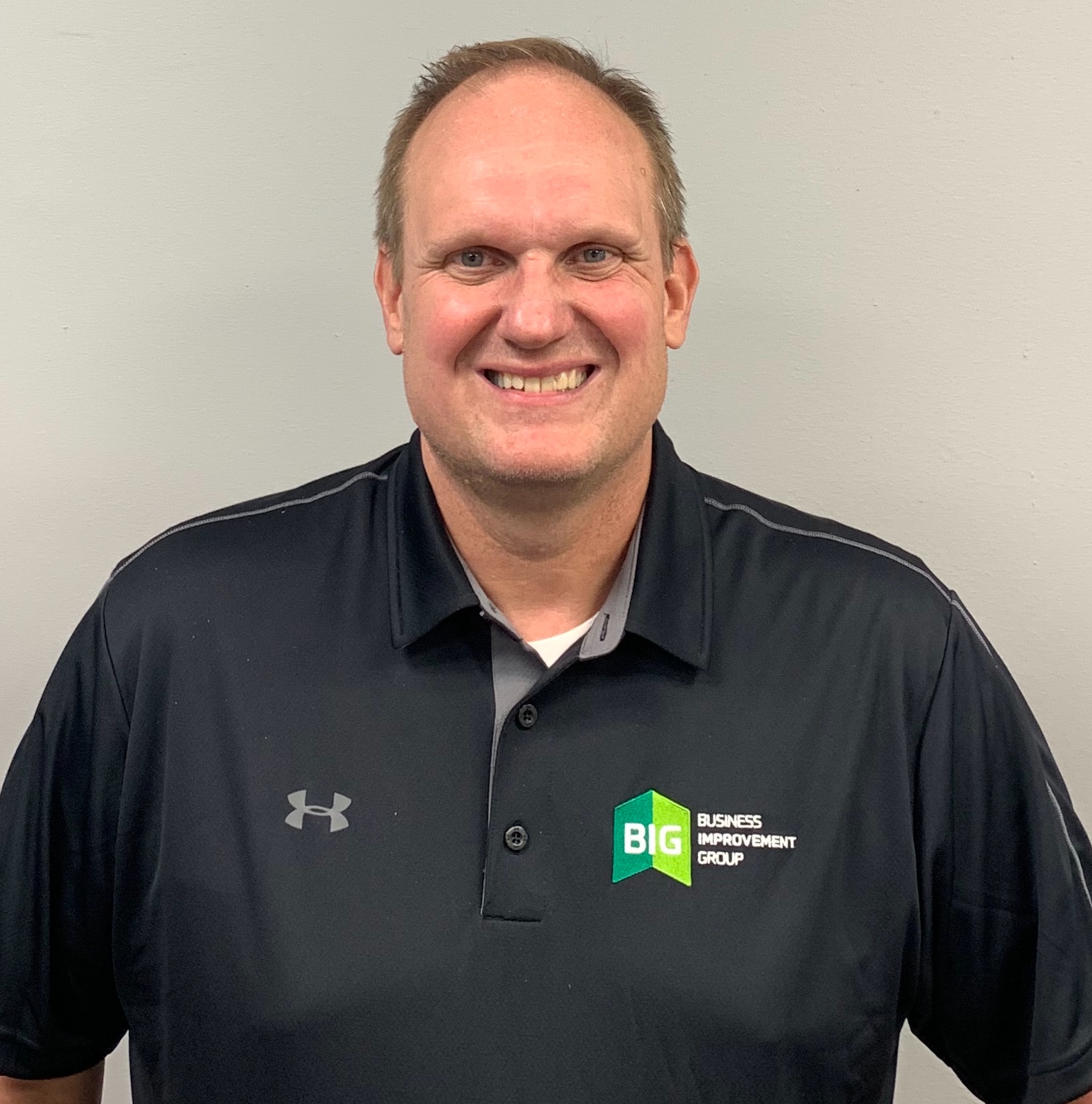
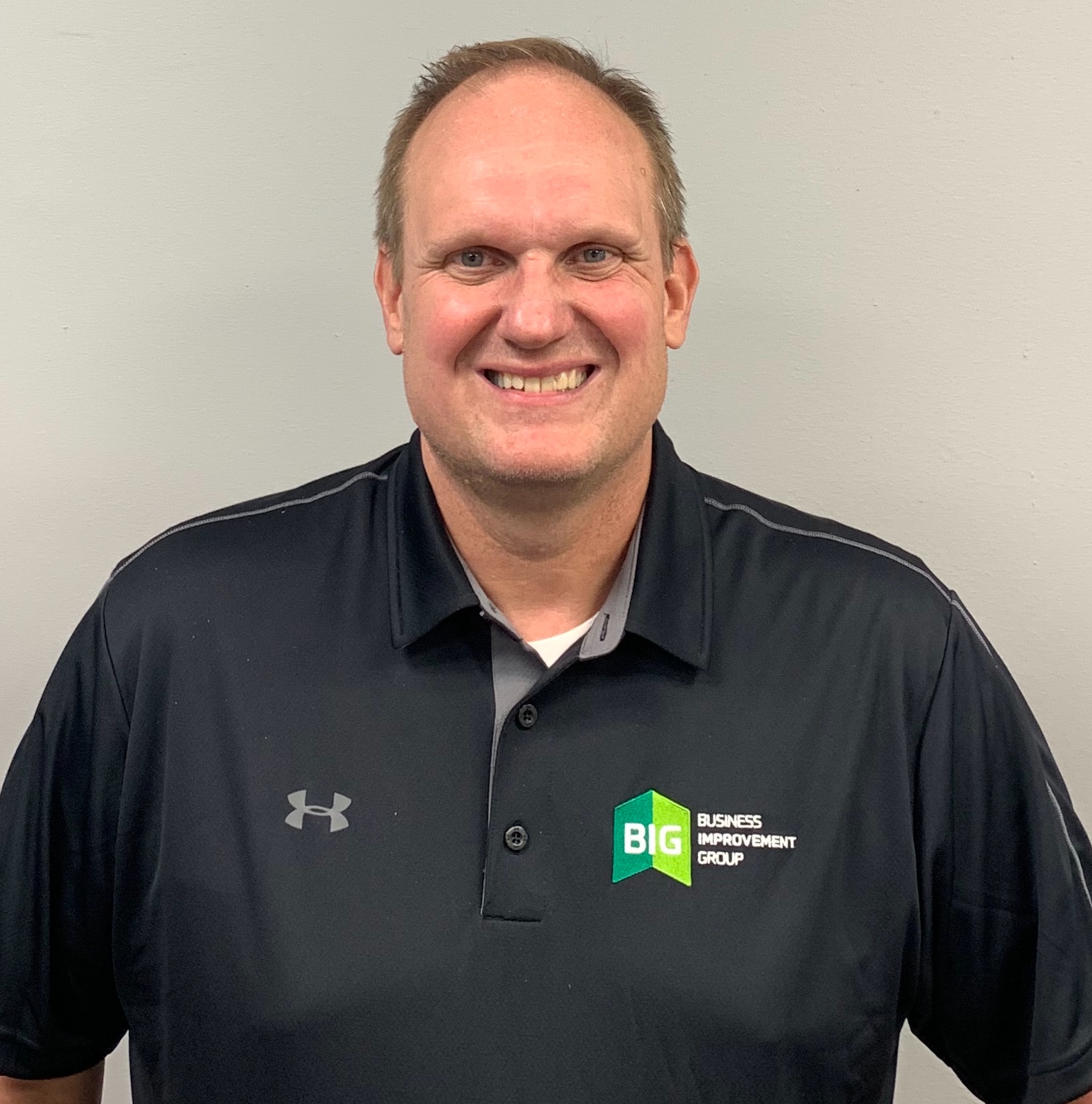
Mike Meyers
Partner and Vice Presidnet of Operations
With over 25 years of manufacturing experience, Mike has filled a variety of leadership roles. At Donnelly Corporation he focused on mastering and implementing the Donnelly Production System (DPS) company-wide. Starting as a Production Supervisor and being promoted to positions of Manufacturing Manager, Operations Manager and Plant Manager, Mike developed his skills for continuous improvement through a combination of comprehensive training sessions and shop floor experiences. He used these techniques and his distinct ability to work with teams to drive change and successfully turn around non-performing plants Mike also supervised the start-up and expansion of a “Greenfield” facility while managing multiple consecutive and concurrent major models launches. During this period, plants he managed were awarded Toyota’s coveted “Most Improved Supplier of the Year.”
In addition to his time at Donnelly, Mike’s comprehensive career experience also includes being Vice President of Operations/ Director of Lean Implementation at a machining and casting corporation where he was responsible for building a complete Lean Enterprise and establishing a culture of continuous improvement in a union environment. Under Mike’s leadership, the company was awarded General Motors “Supplier Quality Excellence” award in recognition of their superior supplier teaming and outstanding customer satisfaction
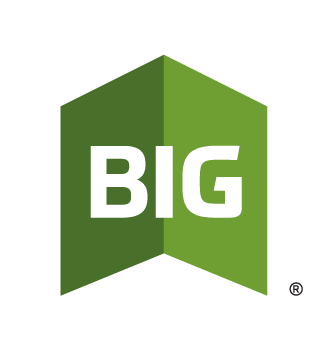
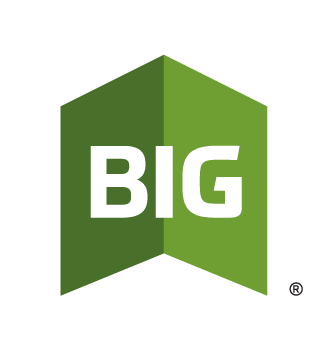
Reach out to Business Improvement Group today and we will be happy to assist you in your next endeavour. Together, we can achieve extraordinary outcomes.